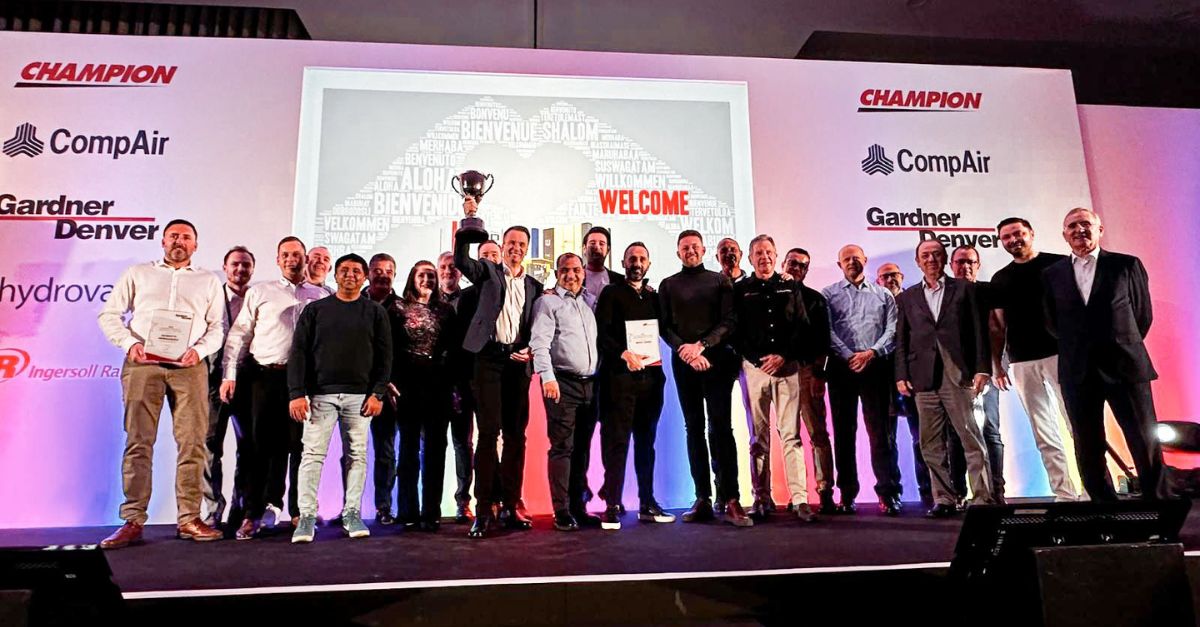
Jsme nejlepším evropským distributorem Ingersoll Rand roku 2024
S hrdostí oznamujeme, že naše společnost byla oceněna jako Nejlepší evropský distributor roku 2024 na celoevropské konferenci distributorů společnosti Ingersoll Rand v Birminghamu ve Velké Británii. Toto prestižní ocenění převzal za naši divizi Kompresory Tomáš Polner.