Do you know anyone who might be interested?
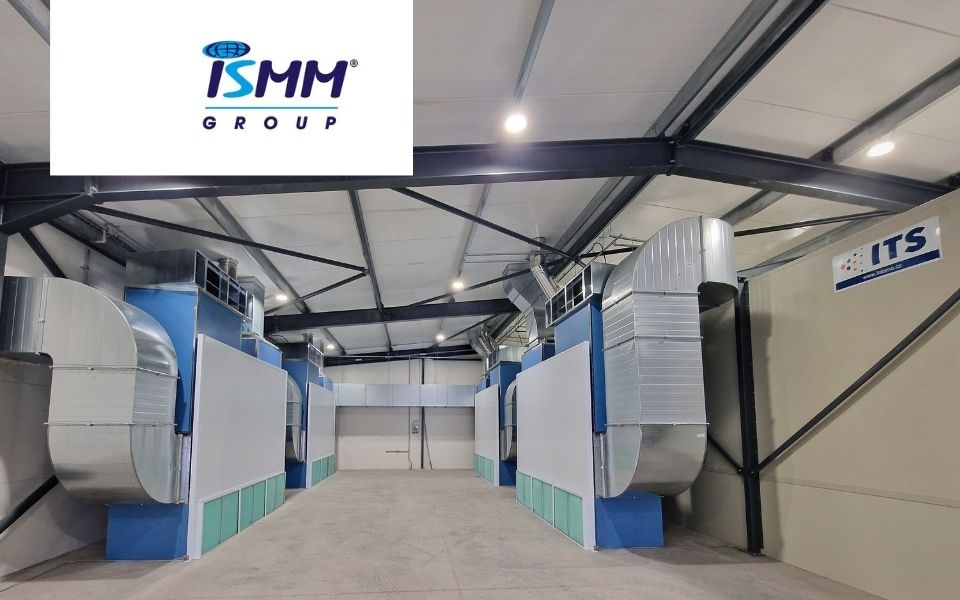
Meeting the demanding requirements from end customers is always very challenging, especially when it comes to the automotive and manufacturing sectors for companies such as Volvo, Claas, or Caterpillar. It was no different in the case of the implementation of an exceptional project with many innovative elements in accordance with the Industry 4.0 concept.
Year of Realization | 2020 |
Location | Čadca (SK) |
Flow profile | 800 x 1400 x 2500 mm (w x h x l) |
Technology |
|
The required parameters for a line capacity of 3 minutes/trolley in all modes and 90 sec./trolley for powder coating were a real challenge. The line was designed as a combined device with a pre-surface treatment with 20 stages based on Zn phosphating in the immersion variant, followed by a KTL node for the application of the base layer. The fully automatic transfer from the immersion part to the Power & Free conveyor system then directs the material to the drying oven. Plenty of positions form a buffer in front of a special node for dividing the trolleys, which run in parallel with immersion, into trolleys following one another through the painting part of the line. Here, it is possible to achieve a clock speed of up to 90 sec./trolley. The Sames quick colour change cab is equipped with full automation for loading product recipes with the SAP ERP system, as well as other parts of the device.
The supply of paint to the powder centre is provided by a mobile robot, which imports paint from the warehouse without an operator and at the same time accurately weighs it. The weight of the consumed paint is accurately recorded in the system, saved to the production order for further calculation and calculation of painting efficiency.
Behind the painting booth is another innovative part of the entire technology. A completely new and unique systemof non-contact robotic measurement of unfired paint, the HiVision DeepControl. The pair of robots not only accurately measure the thickness of the paint with an accuracy of +/- 5 µm, but also store all the parameters for the products in a database. Automatic correction of the spraying system in the case of below/above-limit values is also absolutely essential. Everything takes place during the full operation of the paint shop. This interactive system ensures a significant reduction in the consumption of powder paints in the order of tens of a per cent, reduces scrap and thus significantly helps meet delivery deadlines. Financial savings can be up to several million euros per year, depending on the size of the operation.
All technologies are strictly designed according to BREF guidelines, which prescribe the use of the best-known technologies/principles (BAT) with regard to the ecology of operation.
The spray box is followed by firing in a conventional gas heating furnace, as well as in a drying oven after KTL painting. Both furnaces are equipped with ecological units with direct heating and low-emission gas burners. Wastewater is disposed of fully automatically. Continuous recording of output parameters meeting the demanding discharge limits is a matter of course.
The Power & Free conveyor system is an important element of the entire line and ensures the transport of products weighing up to 400 kg/trolley at a rate of max. 3 minutes. It is equipped with automatic switches, stations for hanging and a suspension system. It allows the transport of products up to 800 x 1400 x 2500 mm.
The complete recipe and work queue is loaded from the company's ERP system into an SQL database, which is used to exchange data with the line. In the same way, the technological data, including, for example, the measured colour thickness, is entered into a database for use in the ERP. It is not a simple communication system, but a big data process. Access to the control is not only local but very easy via the cloud interface from any PS or mobile device. Accessories and peripherals such as a neutralization station, air handling unit, boiler room, demineralized water production, or backup units form one separate unit that can be easily controlled and its operation evaluated efficiently thanks to integrated HiVision modules. The HiVision control system is a registered trademark of ITS.
The above project was implemented in a record time of 3 months and commissioned on the agreed date and is clearly one of the most technologically advanced technologies in the field.
Show more information - Coating facilities
View productDo you know anyone who might be interested?