Do you know anyone who might be interested?
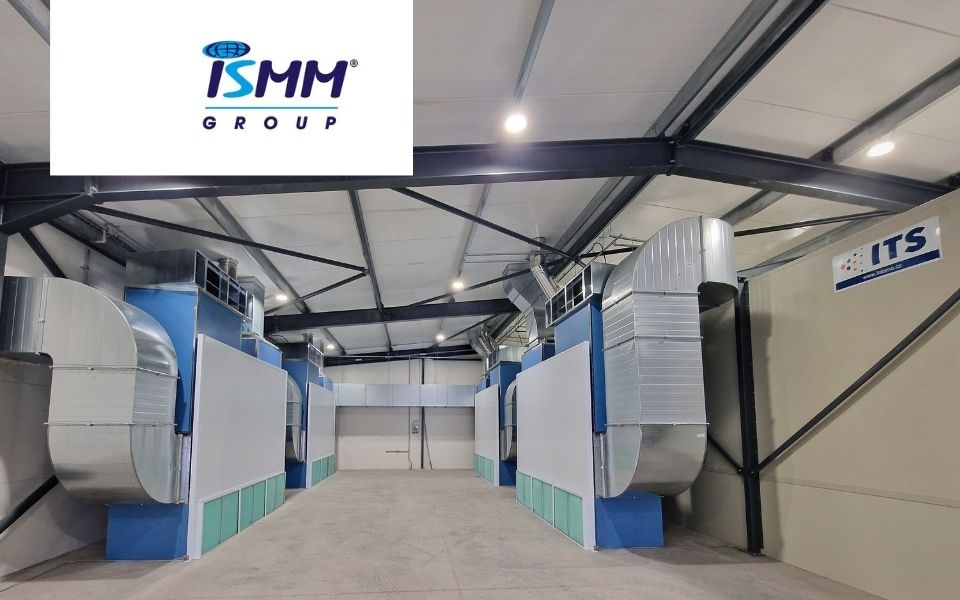
The unique feature of the project, automatic line for passivation of aluminium parts, is operation with a closed-cycle of waste and rinse water, its treatment and return to the process.
Customer | VALEO VÝMĚNÍKY TEPLA, s.r.o. |
Year of Realization | 2021 |
Location | Žebrák (CZ) |
Industry | automotive |
Flow profile | 2.200 x 1.500 x 200 mm |
Max. weight of the product | 900 kg |
Technology |
|
For our client in the automotive industry we have implemented an automatic line for passivation of the surface of aluminium parts, where the applied passivation layer increases adhesion of the glue applied in the following process. Aluminium parts are inserted into transport baskets, their handling between the tubs, loading and unloading into the passivation line are provided by two-axis manipulators that move on steel structure above the tubs. The capacity of the technology is 1 million treated pieces per year.
Closed water cycle
Given process produces waste rinse water that is neutralized. Waste from neutralization is collected in an automatic filter press and it is disposed of as solid waste by external removal. Water is further processed in the evaporation station. Vacuum evaporator has the capacity of 3500 l/hour. It is the biggest installed evaporation station in Central Europe. The distillate from evaporation station returns to the passivation line. Water that is removed from the system in the form of a concentrate, evaporate, etc. is added to the system through reverse osmosis. Reverse osmosis modifies the water parameters to required conductivity. Drying of the parts after pre-treatment is provided by two electrically heated ovens. Evaporated water is discharged into the outside by a fan.
Cooling
There are two positions available for cooling of the parts. The cooling medium is purified air supplied from the outside in the volume of 3000 m3/hour. Equal volume is then discharged by the second fan. The air handling unit is used for replenishing the air that is exhausted from the technology space during the process. Air is heated electrically in winter.
Show more information - Coating facilities
View productDo you know anyone who might be interested?